Zo bouwen we de afzinkelementen voor de Maasdeltatunnel
Een uitdaging? Dat is nog zacht uitgedrukt. In een reusachtig droogdok in Rotterdam maken we twee tunnelelementen van ongeveer 200 meter lang, 42 meter breed en 8 meter hoog.
Midden in het droogdok kijkt Fern van Efferink om zich heen. “Eigenlijk zou je hier iedere week langs moeten komen om de grote veranderingen te zien. Hier gebeurt zo veel. Op een heel klein oppervlak.”
Vanuit zijn rol als Werkvoorbereider staat iedere werkdag van Fern in het teken van deze twee elementen. Hij bereidt de werkzaamheden voor, stemt keuzes af met collega’s en partners en - niet onbelangrijk - loopt buiten een rondje om de elementen te zien groeien. Het is een spraakmakende operatie. Of, zoals Fern zegt: “Zo’n bouwterrein is écht mooi om te zien.”
We zetten zes van de grootste bijzonderheden van de afzinkelementen op een rij:
#1: Van zes naar twee elementen
We gaan een paar jaar terug in de tijd. Tijdens het aanbestedingstraject verdiepte consortium BAAK, een combinatie van Ballast Nedam, DEME en Macquarie Capital, zich in het referentieontwerp van Rijkswaterstaat. Doordat de afzinktunnel in het drukke havengebied van Rotterdam komt te liggen, is de omgeving en uitvoering gebaat bij een werkwijze met weinig hinder en weinig risico’s voor de planning. Consortium BAAK kwam daarom met een alternatief plan waarbij verschillende oplossingen zijn gecreëerd voor de complexe elementen uit het referentieontwerp. In dit plan is de lengte van het afgezonken gedeelte van de tunnel verkleind, waardoor we de Maasdeltatunnel kunnen bouwen met twee grotere afzinkelementen, in plaats van zes kleinere. Dit scheelt vier grote afzinkoperaties, wat zorgt voor minder hinder voor de scheepvaart en minder risico op planningswijzigingen. Na het afzinken sluiten de elementen aan op de landhoofden aan de oever, die volgens dit ontwerp dieper en verder in de rivier het Scheur worden gebouwd.
#2: Groots bouwen op klein terrein
Echt klein is het Damen Verolme droogdok in Rotterdam niet te noemen, maar met de twee gigantische afzinkelementen is het toch al gauw vol. Het droogdok ligt op een steenworp afstand van onze bouwplaats in Rozenburg. Door de omvang van de elementen hebben we beperkt de ruimte om onze werkzaamheden uit te voeren en daarom is efficiënt werken een vereiste.
We werken niet alleen efficiënt, maar ook snel. De bouw van de afzinkelementen startte in juni 2021 en is naar verwachting begin 2022 klaar. Na de bouw sluiten we de elementen af met stalen kopschotten en gaan we ze in het relatief kleine droogdok opdrijven en de speelruimte opzoeken. We draaien de elementen dan een klein beetje, zodat we ze één voor één kunnen uitvaren. Vervolgens worden ze in de naastgelegen haven geparkeerd, waar de tunnelelementen gereed worden gemaakt voor het afzinken. Van daaruit worden ze voor de afzinkoperatie naar het Scheur getransporteerd en afgezonken.
#3: Parallel werken
De bouw van de afzinkelementen is opgebouwd in onderdelen, ook wel ‘moten’ genoemd. Element Noord bestaat uit acht moten en element Zuid heeft er zeven. Van iedere moot storten we eerst de vloer, dan de tussenwanden tussen de rijkokers en tot slot de buitenwanden en het dak. In drie keer beton storten wordt dus één moot van het element gemaakt. Handig, want dat gaat snel én zorgt voor zo min mogelijk stortvoegen tussen de verschillen de delen. Deze werkwijze biedt een perfecte gelegenheid voor een learning curve, want door de repeterende werkzaamheden loopt de bouwtrein steeds soepeler.
Een moot bouwen we in een cyclus van twee weken. Hierdoor zit er één week verschil tussen de voortgang van het tunnelelement van de noordelijke en het tunnelelement van de zuidelijke oever. De bouw van de twee tunnelelementen loopt hierdoor met elkaar in de pas en daarnaast creëren we een ‘eigen’ stortdag voor elk onderdeel. Op woensdag storten we van het ene element een vloerdeel, op donderdag de middenwanden en op vrijdag een wandendakdeel. De week daarna doen we precies hetzelfde bij het andere element.
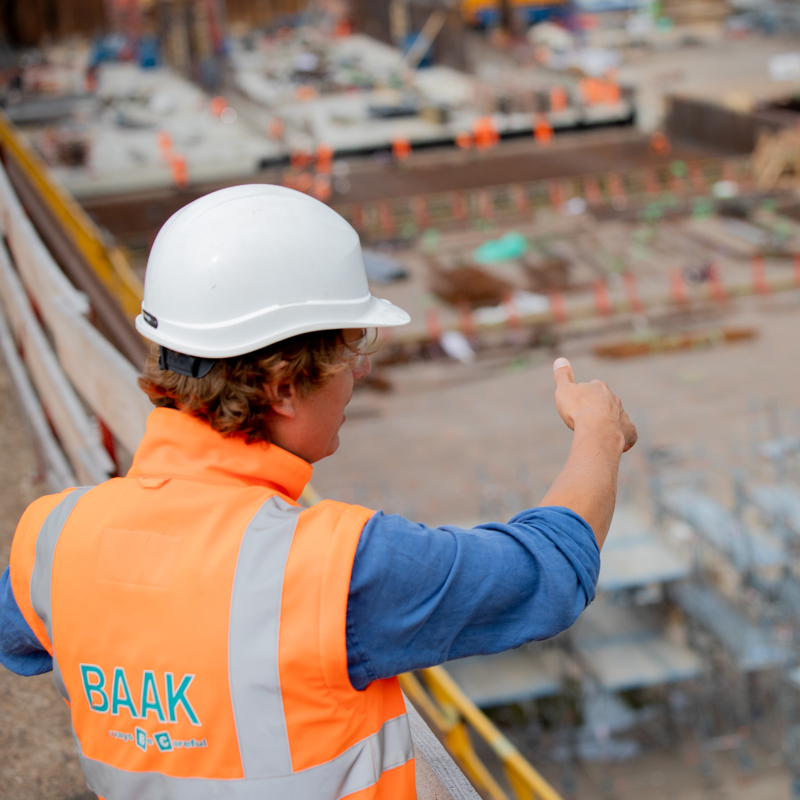
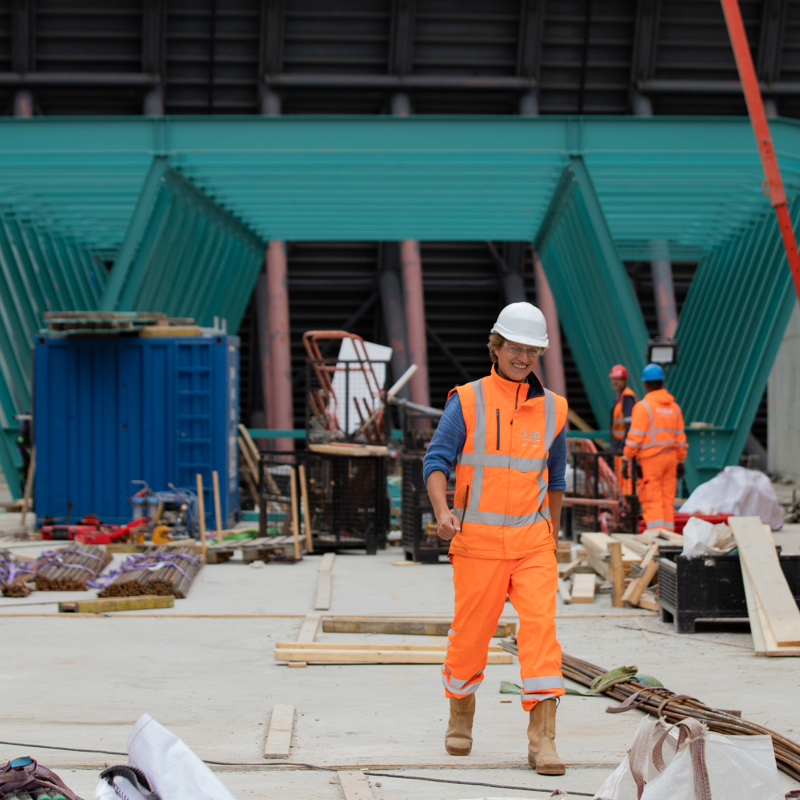
#4: Een extra koker
Afzinkelementen moeten altijd een bepaald gewicht hebben waardoor ze kunnen blijven drijven wanneer dat nodig is én op hun plek kunnen blijven zodra ze zijn afgezonken. Daarom voegen we tijdens de bouw extra gewicht toe, zodat we precies met het juiste gewicht werken. De vraag is: waar komt dat gewicht? De boven- en onderzijdes vallen af, aangezien we geen extra hoogte aan de elementen kunnen toevoegen. Deze hoogte kent namelijk een limiet, aangezien de elementen aan beide oevers moeten aansluiten op de andere tunneldelen.
De oplossing is als volgt: Aan de zijkant bouwen we een extra koker die we later volstorten met beton. Tijdens het bouwen van deze extra koker denken we al na over de volgende bouwfases van de tunnel. Moeten we leidingen alvast instorten? Willen we voorzieningen aanbrengen? Of blijft het bij enkel beton? Deze keuzes hebben we gemaakt tijdens het ontwerpproces.
#5: Deze voorspanning zie je niet vaak
Door de voorspanning in dwarsligging is het ontwerp lager en smaller. Dit werkt als volgt: we nemen kokers op in de vloeren en het dak van het afzinkelement. Na de betonstort worden daar strengen ingeschoten. Als het beton hard genoeg is, worden deze strengen met zware vijzels aangetrokken en op spanning gebracht. Daarna kunnen we het laatste stukje van de vloer afmaken, ook wel ‘de teen’ genoemd.
#6: Samenwerking met Strukton
Het bouwen van deze afzinkelementen doen we niet alleen. Naast Ballast Nedam speelt consortiumpartner DEME een belangrijke rol bij de afzinkoperatie. Hierbij wordt het consortium BAAK bovendien bijgestaan door Strukton. Dit zogenoemde 'A-Team' is al sinds de start van de tender betrokken bij de bouwplannen en het ontwerp en werkt aan een optimale uitvoering van het afzinken. Eén van de keuzes die we dankzij deze samenwerking hebben gemaakt is het kiezen van stalen kopschotten, waarmee we de tunnelelementen voor het afzinken kunnen dichtzetten. Zo kunnen we de elementen gemakkelijk laten opdrijven wanneer die dag is aangebroken.
Als je het eenmaal door hebt, laat het je niet meer los
'Echt een specialisme'
Tot aan het begin van 2022 wordt in dit droogdok hard gewerkt aan de twee afzinkelementen. Daarna, wanneer de elementen verderop liggen te dobberen, wachten we tot onze collega’s op de noord- en zuidoever klaar zijn met het bouwen van de landhoofden. Vervolgens starten we de langverwachte afzinkoperatie waarbij de elementen op hun plek worden gelegd, op zo’n 27 meter diepte. En dan? Na de nodige werkzaamheden aan de technische installaties, wegenbouw en afbouw, is de nieuwe Maasdeltatunnel een feit.
“Afzinktunnels bouwen is echt een specialisme”, zegt Fern. “En als je het eenmaal door hebt, laat het je niet meer los. Eigenlijk is het simpel. We bouwen een koker, een grote schoenendoos. Tegelijkertijd werken we continu op de weegschaal van de zwaartekracht en de wet van Archimedes. Dat maakt het zo mooi.”